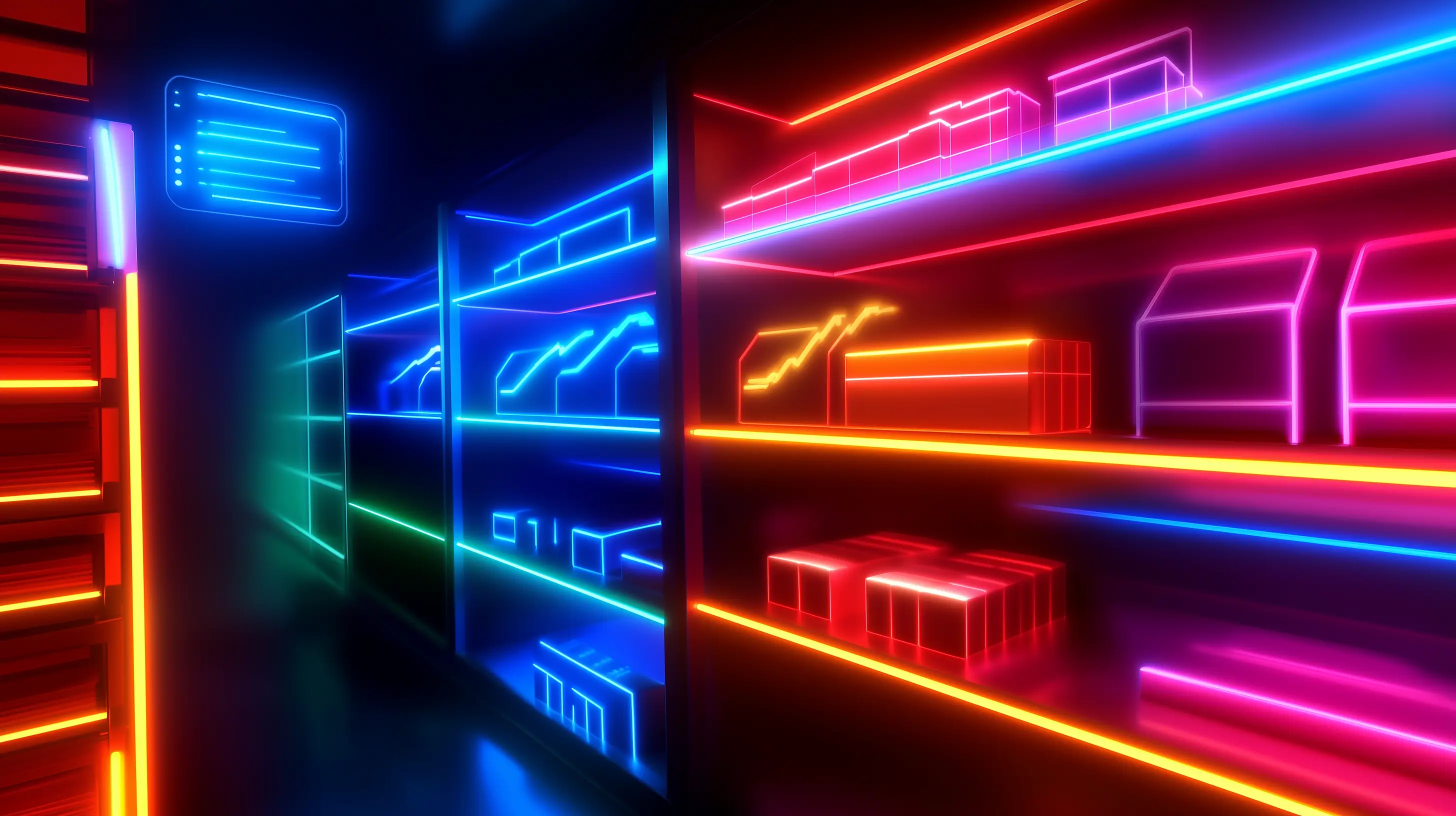
Inventory Management Automation
Identifying the Problem
EcoGrocers, a regional grocery chain, struggled with inconsistent inventory management. Overstocking led to increased waste of perishable goods, while frequent stockouts of high-demand items caused customer dissatisfaction. Their existing manual tracking systems were inadequate for handling the complexity of their operations.
Project Objectives
The main goals were to:
- Optimize inventory levels by accurately predicting demand trends.
- Reduce waste of perishable items through smarter stock replenishment.
- Ensure availability of top-selling products during peak periods.
Crafting the Solution
NeonFlow created a dynamic inventory management system powered by AI. Key features included:
- Sales Trend Analysis: Leveraged historical sales data to identify seasonal and regional purchasing patterns.
- Real-Time Inventory Tracking: Monitored stock levels across all locations and flagged potential shortages.
- Automated Reordering: Triggered purchase orders for high-demand items when inventory fell below optimal levels.
Implementation Steps
- Data Integration: Combined sales, inventory, and supplier data into a unified system.
- Algorithm Development: Built predictive models using machine learning to forecast demand with high accuracy.
- Dashboard Deployment: Delivered a user-friendly interface for store managers to monitor stock levels and system suggestions.
Key Results
The AI system delivered measurable improvements:
- 25% reduction in inventory holding costs.
- 20% increase in stock availability for fast-moving items.
- Minimized perishable item waste by aligning orders with actual demand patterns.
Client Feedback
EcoGrocers praised the system for its precision and ease of use, highlighting its immediate impact on operational costs and customer satisfaction.
Key Insights
This project showcased how data-driven automation can revolutionize inventory management, benefiting both businesses and their customers.